Understanding Tooling Molding: A Comprehensive Guide for Metal Fabricators
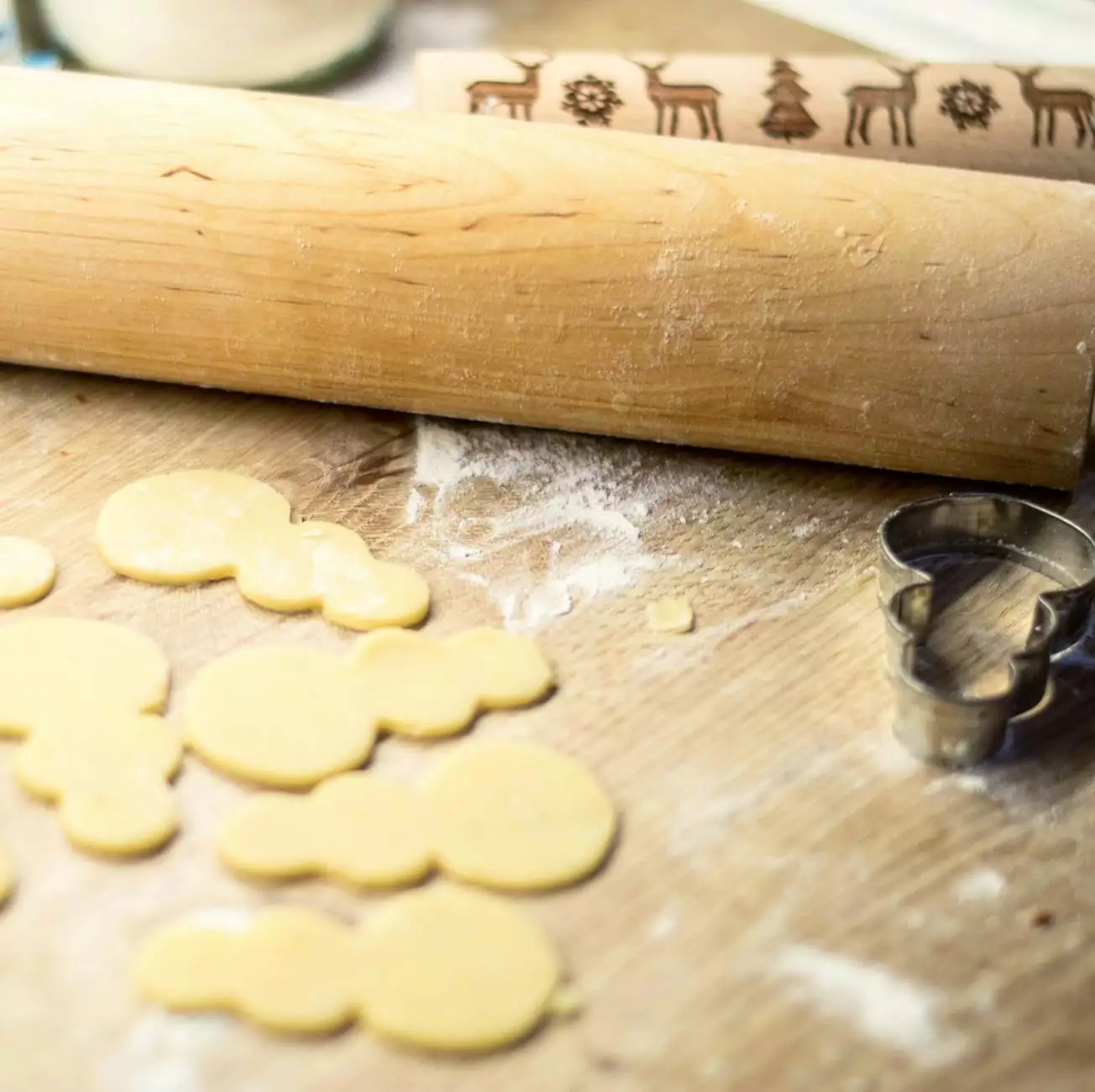
In the realm of metal fabrication, achieving the perfect design and functionality of components hinges significantly on the processes involved in production. One of the most critical processes is tooling molding, a technique that transforms raw materials into the high-quality products needed across various industries. In this article, we will explore the intricacies of tooling molding, its applications, benefits, and why companies like Deep Mould are at the forefront of this essential process.
What is Tooling Molding?
Tooling molding is a manufacturing process that involves the shaping of materials by utilizing molds. It is a versatile production method widely used for creating complex and intricate parts from metals and plastics. The process can be broken down into several key stages, including:
- Designing the Mold: This is the initial stage where designers create a detailed 3D model of the part to be produced.
- Fabricating the Mold: Once the design is finalized, skilled craftsmen fabricate the mold using high-quality materials to ensure durability and precision.
- Heating and Injection: The selected material is heated until it reaches a liquid state and then injected into the mold.
- Cooling and Finishing: After the material solidifies, the mold is opened, and the part is ejected. Any finishing touches are applied to meet specifications.
The Importance of Tooling Molding in Metal Fabrication
Tooling molding plays a pivotal role in metal fabrication. Here are some compelling reasons why:
- Precision Engineering: The tooling molding process enables manufacturers to achieve high precision in their products, which is crucial in industries like automotive, aerospace, and electronics.
- Reduced Waste: Efficient molding processes minimize material waste, contributing to a more sustainable production model.
- Cost-Effectiveness: Although the initial investment in molds can be substantial, the long-term benefits of mass production often outweigh these costs.
- Design Flexibility: Tooling molding allows for the production of intricate designs that may not be possible with traditional machining methods.
Applications of Tooling Molding
The applications of tooling molding are vast and varied. Some key sectors that benefit from this technology include:
- Aerospace: Critical components in aircraft manufacturing rely on the precision and durability provided by tooling molding.
- Automotive: The automotive industry uses tooling molding to produce everything from engine parts to body panels with optimal efficiency.
- Electronics: Housing and component parts for electronic devices often utilize custom molds for high precision.
- Consumer Products: From household appliances to toys, many consumer goods undergo tooling molding to enhance design and utility.
Advantages of Using High-Quality Tooling Molding Services
Engaging a qualified tooling molding service, such as Deep Mould, offers numerous advantages:
1. Expertise and Experience
With years of experience in metal fabrication, Deep Mould offers unmatched expertise. Their skilled technicians understand the nuances of tooling molding, ensuring your products meet the highest standards.
2. Advanced Technology
Deep Mould utilizes cutting-edge technology and equipment that enhances production efficiency and product quality, allowing clients to stay competitive in their respective markets.
3. Customization
Every project is unique, and Deep Mould excels in providing tailored solutions that meet your specific needs. Custom molds are designed to fit your product perfectly, resulting in improved performance.
4. Quick Turnaround Times
In today’s fast-paced market, timing is everything. Deep Mould’s efficient processes ensure that you receive your components on time without compromising quality.
Challenges in Tooling Molding and How to Overcome Them
While tooling molding offers significant benefits, it also presents certain challenges. Being aware of these challenges helps mitigate risks and assure smooth operations.
Material Selection
One of the primary challenges is choosing the right material for both the molds and the products. Collaborating with experts at Deep Mould can guide you in selecting materials that offer the best performance and cost-effectiveness.
Mold Maintenance
Regular maintenance of molds is necessary to extend their lifespan and ensure consistent quality. Deep Mould places strong emphasis on mold maintenance, employing best practices that enhance durability.
Complex Designs
As designs become increasingly intricate, creating molds that capture fine details can be challenging. Advanced simulation software and manufacturing techniques employed by Deep Mould help overcome these hurdles.
Future Trends in Tooling Molding
The field of tooling molding is rapidly evolving. Some emerging trends for the future include:
- 3D Printing: The integration of 3D printing technology is revolutionizing how molds are designed and produced, allowing for rapid prototyping and reduced lead times.
- Sustainability Efforts: Increasing focus on sustainable practices is pushing manufacturers to seek environmentally friendly materials and processes.
- Automation: Automation in tooling molding processes enhances efficiency, consistency, and worker safety by reducing labor-intensive tasks.
Conclusion: The Role of Tooling Molding in Modern Manufacturing
In conclusion, tooling molding stands as a cornerstone of the metal fabrication industry. The precision, efficiency, and adaptability it offers are invaluable to manufacturers in various sectors. Partnering with a proficient company like Deep Mould ensures that you leverage the full potential of tooling molding, optimizing both your production processes and product quality. As the industry continues to innovate and evolve, those who embrace these advancements will undoubtedly lead the market forward.
We invite you to explore the world of tooling molding and discover how it can transform your production needs. For more information on how Deep Mould can assist you with your metal fabrication projects, please visit our website at deepmould.net.